More than 60% of executives report that their continuous improvement initiatives have delivered only minimal financial impact. These initiatives have proven to be costly, resource intensive, lengthy to implement, and have not delivered the dramatic performance improvement that leaders expected.
So why have they failed?
Research and analysis reveal three reasons traditional Operational Excellence initiatives are ineffective in today’s complex world:
1. Traditional approaches create organizational complexity by failing to define Operational Excellence in a simple, clear, and actionable way that allows the organization to unite around a common objective.
The critical first step in achieving Operational Excellence is to understand what the term means, while utilizing a clear and concise definition. Unfortunately, most firms either completely overlook this step or dramatically underestimate the difficulty of aligning on a clear and concise definition of Operational Excellence.
Failure to clearly define and understand Operational Excellence results in inconsistent, ambiguous, and even confusing messages. This makes it difficult for employees to understand what they are trying to achieve, leading to a wasted effort and lack of commitment.
2. Traditional methodologies take a bottom-up approach to developing the plan for achieving Operational Excellence, rather than a top-down approach that cuts through organizational and process complexity.
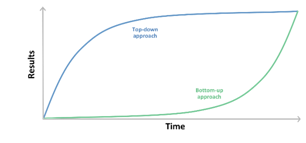
Delivering transformative results is much easier using a top-down approach rather than the process-by-process improvements that are seen with traditional methodologies. A key benefit is that top-down approaches can be done with fewer resources and in less time since they focus on areas of greatest impact.
3. Traditional approaches attempt to improve process and organizations first, and then establish control. Control over key processes is the foundation, not the result.
Experienced practitioners of process improvement methodologies understand the importance of establishing control of a process before attempting to improve it. Until a process is under control it is impossible to understand its true capabilities. You can’t implement effective changes to improve performance without first understanding and managing, the sources of variation. Nevertheless, the structure of most methodologies leads those who are less experienced, to immediately start with improvement.